Comprehensive Guide to Plastic Injection Mold Tooling: Unlocking Precision and Efficiency in Modern Manufacturing
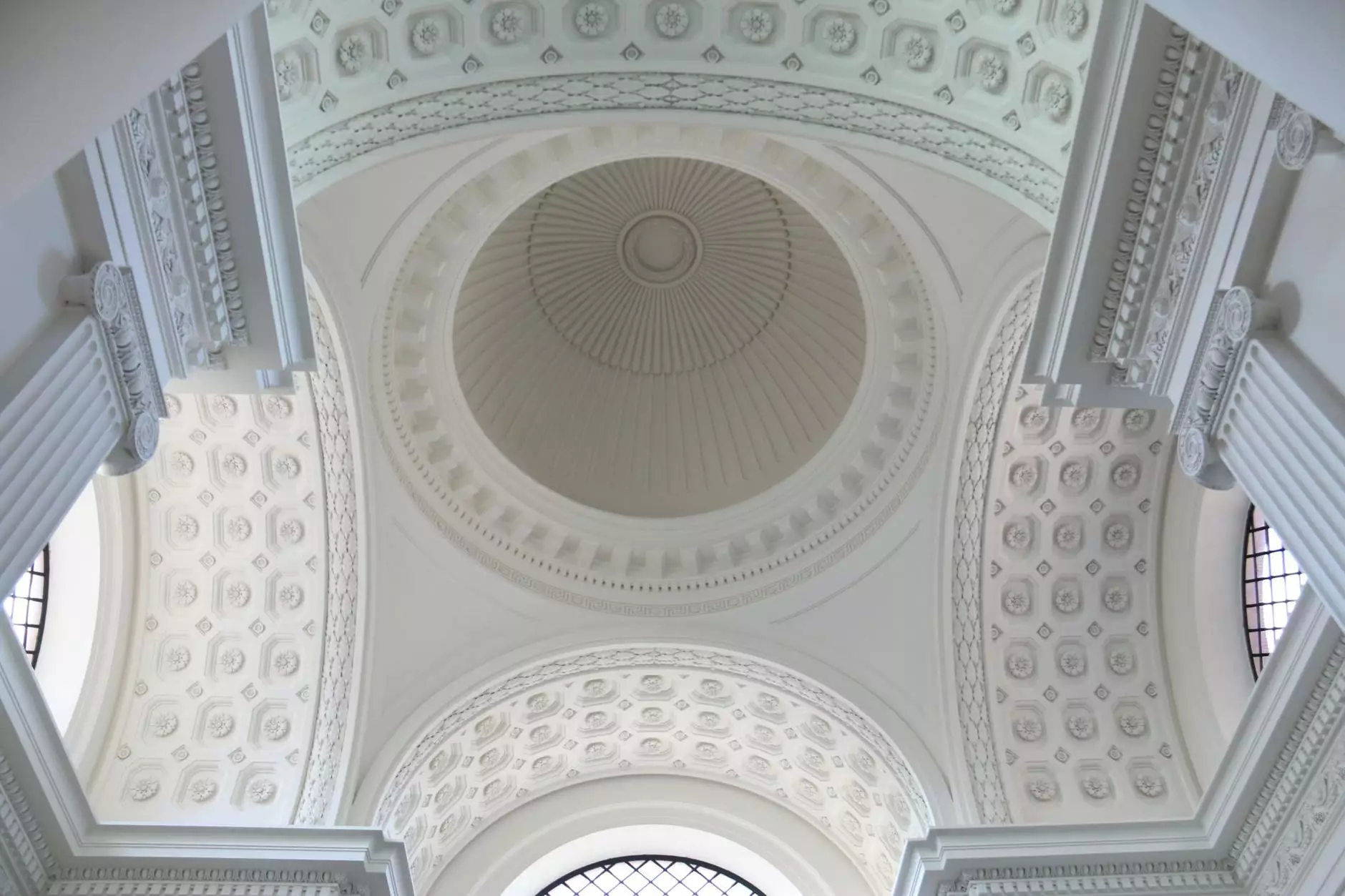
In today’s rapidly evolving manufacturing landscape, plastic injection mold tooling stands as a cornerstone technology enabling the production of complex, high-precision plastic components. As a chief component in the manufacturing pipeline, the quality, durability, and efficiency of injection molds directly influence the success of mass production processes. This detailed guide explores every facet of plastic injection mold tooling, from fundamental principles to advanced manufacturing techniques, empowering engineers, manufacturers, and industry stakeholders to optimize their operations and achieve superior results.
Understanding Plastic Injection Mold Tooling: The Foundation of Modern Manufacturing
Plastic injection mold tooling refers to the specialized equipment designed to produce plastic parts via the injection molding process. This process involves injecting molten plastic into a precisely engineered mold cavity, allowing it to cool and solidify into the desired shape. Accurate tooling is vital for ensuring consistent quality, dimensional accuracy, and efficient production cycles.
The Significance of High-Quality Plastic Injection Mold Tooling
Investing in top-tier plastic injection mold tooling translates into numerous benefits, including:
- Enhanced Product Precision: Achieving tight tolerances necessary for modern applications.
- Higher Production Efficiency: Reducing cycle times and minimizing scrap rates.
- Longer Mold Lifespan: Reducing downtime and maintenance costs over the manufacturing lifecycle.
- Cost-Effectiveness: Lower per-part costs due to high durability and repeatability.
Design Considerations for Advanced Plastic Injection Mold Tooling
The effectiveness of plastic injection mold tooling hinges on meticulous design. Critical aspects include:
- Mold Material Selection: Opting for durable metals like H13, P20, or stainless steel to withstand high pressures and repeated cycles.
- Mold Structure: Incorporating core & cavity design, ejection mechanisms, and cooling channels for uniform heat dissipation.
- Part Geometry and Draft Angles: Ensuring ease of ejection and minimizing defect rates.
- Gate and Runner Design: Optimizing flow paths to prevent defects and improve cycle times.
- Surface Finish: Achieving desired aesthetic and functional surface qualities through polishing or texturing.
Advanced Manufacturing Techniques in Plastic Injection Mold Tooling
Modern plastic injection mold tooling harnesses advanced manufacturing technologies such as:
- CNC Machining: For high precision component fabrication and complex geometries.
- Electrical Discharge Machining (EDM): For intricate cavity features and fine details.
- 3D Printing: For rapid prototyping and mold insert creation, reducing lead times.
- Surface Engineering: Techniques like PVD coating and texturing to enhance mold performance and part aesthetics.
Material Selection for Durable and Efficient Plastic Injection Mold Tooling
Choosing the right materials for plastic injection mold tooling is essential for longevity and performance. Common materials include:
- H13 Steel: Known for toughness, heat resistance, and machinability, ideal for high-volume production.
- P20 Steel: Popular for prototype and medium-run molds due to its ease of machining.
- Stainless Steel: Offers corrosion resistance, suitable for molds requiring frequent cleaning.
- Carbide: For inserts and components demanding exceptional wear resistance.
Economic Benefits of High-Quality Plastic Injection Mold Tooling
While initial tooling costs can be significant, high-quality plastic injection mold tooling offers remarkable economic advantages, including:
- Reduced Production Costs: Longer mold longevity diminishes the need for frequent replacements.
- Consistent Product Quality: Minimizes defects and rejection rates, saving material and labor costs.
- Faster Time-to-Market: Efficient processes and rapid prototyping accelerate development cycles.
- Lower Maintenance Expenses: Durable molds require less downtime and repairs.
Partnerships and Expertise in Plastic Injection Mold Tooling
Partnering with experienced mold manufacturers like DeepMould offers strategic advantages:
- Design Optimization: Leveraging expert insights to refine mold concepts for manufacturability.
- Material and Process Selection: Applying best practices to enhance durability and finish.
- Prototyping and Testing: Rapid iterations to validate molds before mass production.
- After-Sales Support: Ongoing maintenance, repairs, and upgrades to maximize mold lifespan.
Innovation and Future Trends in Plastic Injection Mold Tooling
The future of plastic injection mold tooling is driven by continuous innovation. Emerging trends include:
- Smart Molds: Integration of sensors and automation for real-time monitoring.
- 3D Printing for Mold Components: Expanding capabilities for complex geometries and rapid prototyping.
- Eco-Friendly Materials and Processes: Reducing environmental impact through sustainable practices.
- Advanced Cooling Techniques: Improving cycle times and part quality through innovative thermal management.
Conclusion: The Cornerstone of Successful Manufacturing
In conclusion, plastic injection mold tooling is more than just a manufacturing tool; it is a strategic asset that determines the quality, efficiency, and profitability of production. Investing in high-quality, precision-engineered molds with advanced materials and manufacturing techniques unlocks significant advantages in today's competitive marketplace. Engaging with knowledgeable partners like DeepMould ensures access to cutting-edge solutions and expert support, ultimately driving your business toward greater success and innovation.
Why Choose DeepMould for Your Plastic Injection Mold Tooling Needs?
DeepMould specializes in providing comprehensive plastic injection mold tooling solutions tailored to meet the specific needs of diverse industries. Our commitment to quality, precision, and customer satisfaction sets us apart:
- Expertise in all aspects of mold design, manufacturing, and testing.
- State-of-the-art manufacturing facilities with advanced CNC, EDM, and finishing equipment.
- Material selection expertise to optimize mold life and performance.
- Fast turnaround times with an emphasis on quality control and reliability.
Partner with DeepMould for premium plastic injection mold tooling that elevates your manufacturing capabilities to the next level, ensuring your products excel in precision, durability, and cost-efficiency.