Understanding Injection Molding Tools: A Comprehensive Guide
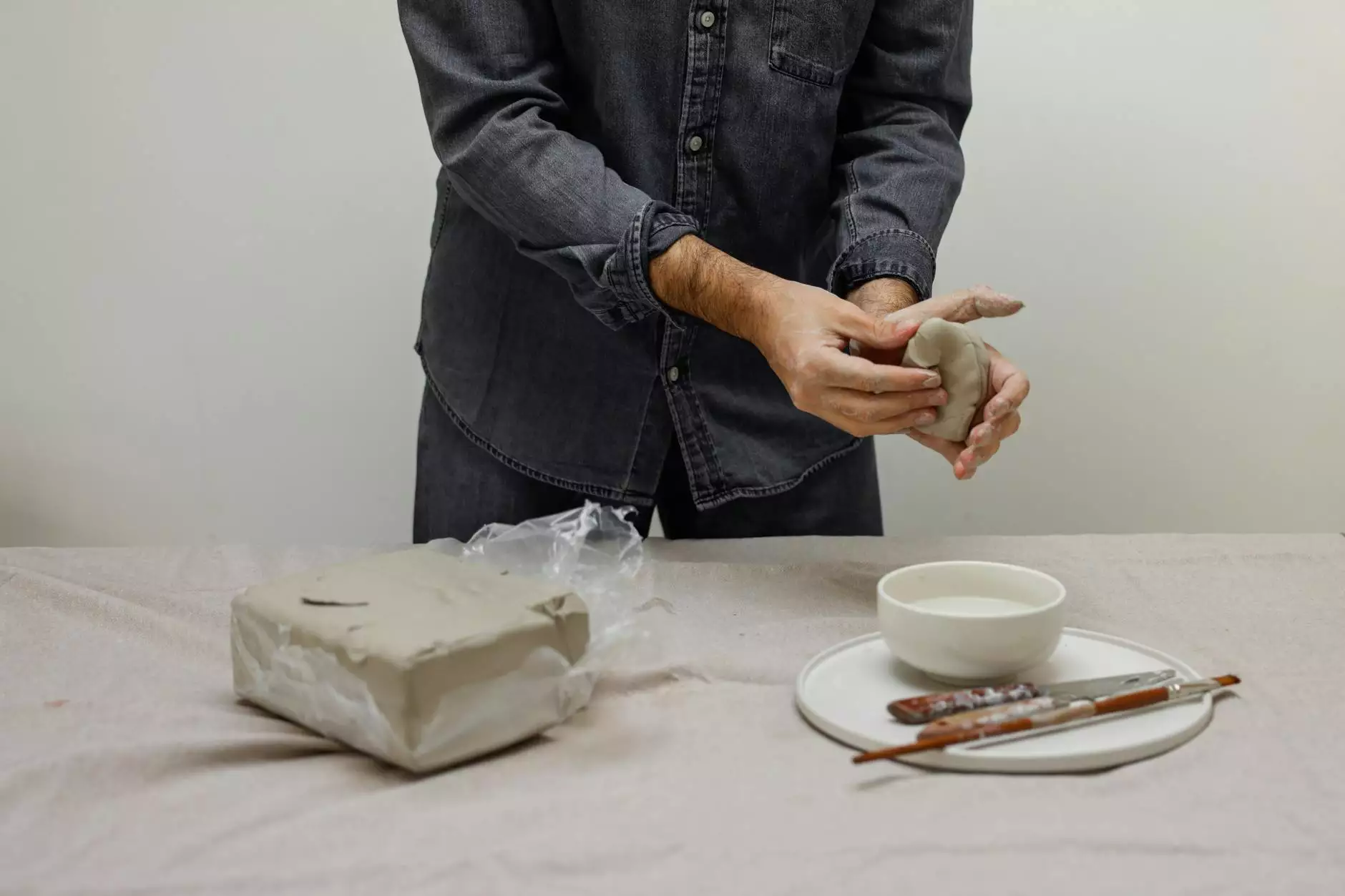
Injection molding tools play a critical role in the manufacturing industry, enabling the production of complex parts with high precision and efficiency. In this detailed guide, we will delve into the various aspects of injection molding tools, providing you with valuable insights into their design, application, and benefits across different sectors, particularly in the realm of metal fabrication.
What is Injection Molding?
Injection molding is a manufacturing process that involves injecting molten material into a mold to create specific shapes. This method is widely used for various materials, including plastics, metals, and ceramics. Among these, injection molding tools are essential for producing consistent, high-quality parts in large quantities.
The History and Evolution of Injection Molding
The origins of injection molding date back to the mid-1800s, with the development of early injection molding machines. Over the decades, this process has evolved significantly, leading to advanced techniques and materials. Today, injection molding is one of the most efficient methods of mass production.
Key Components of Injection Molding Tools
Understanding the components involved in injection molding tools is crucial for their effective application. Here are the primary elements:
- Mold Cavity: The hollow space that shapes the molten material into the desired form.
- Mold Core: Works in conjunction with the mold cavity to define the internal features of the product.
- Injection Unit: The mechanism that melts the raw material and injects it into the mold.
- Cooling System: Responsible for cooling the injected material to form a solid structure before ejection.
- Ejection System: Facilitates the removal of the finished product from the mold.
Types of Injection Molding Tools
Different types of injection molding tools are designed to cater to various manufacturing needs:
1. Single Cavity Molds
These molds contain just one cavity, allowing for the production of one part at a time. They are ideal for low-volume production runs.
2. Multi-Cavity Molds
As the name suggests, these contain multiple cavities, enabling the simultaneous production of several identical parts, significantly increasing efficiency for high-volume production.
3. Family Molds
Family molds allow different components to be produced in a single cycle. This is particularly useful for products that require several parts to work together.
4. Hot Runner Molds
Hot runner systems keep the plastic material heated within the mold, reducing waste and cycle times for consistent quality across multiple shots.
5. Cold Runner Molds
In contrast, cold runner molds allow the material to cool before it reaches the part, leading to waste but often a simpler design and lower upfront costs.
Benefits of Using Injection Molding Tools
The advantages of utilizing injection molding tools are extensive:
- High Efficiency: Injection molding enables rapid production cycles, making it suitable for large-scale manufacturing.
- Consistency: The process ensures uniform products with tight tolerances, reducing defects and variability.
- Complex Designs: Intricate shapes and features can be created that would be challenging with other manufacturing methods.
- Material Versatility: Injection molding can accommodate a wide range of materials, including thermoplastics and thermosets.
- Reduced Waste: The precision of the process minimizes excess material, which is often reclaimable for future use.
Applications of Injection Molding Tools in Metal Fabrication
While injection molding is often associated with plastics, it also extends to the fabrication of metal parts. Here are some key applications:
1. Automotive Industry
Injection molding is extensively used to produce various automotive components, such as dashboards, interior panels, and housings. The precision and durability of molds ensure that parts meet stringent safety and performance standards.
2. Consumer Electronics
From smartphone casings to laptop components, injection molding tools are fundamental in producing lightweight and durable parts that enhance the performance and aesthetics of consumer electronics.
3. Medical Devices
In the medical field, injection molding is vital for manufacturing components like syringes, casings for instruments, and even complex medical devices that require high precision and hygiene standards.
4. Industrial Equipment
Heavy machinery and equipment often utilize molded plastic and metal parts that are produced via injection molding, highlighting the method's reliability in industrial applications.
The Process of Injection Molding: Step-by-Step
The injection molding process consists of several steps:
1. Material Preparation
The raw material, typically in pellet form, is prepared and measured before being fed into the injection unit.
2. Melting
The pellets are then heated to their melting point, creating a molten material suitable for injection.
3. Injection
The molten material is injected into the mold cavity under high pressure.
4. Cooling
Once injected, the material is allowed to cool and solidify, taking the shape of the mold.
5. Ejection
After cooling, the ejection system removes the completed part from the mold, making it ready for further processing or assembly.
Choosing the Right Injection Molding Tool Supplier
When selecting a supplier for injection molding tools, consider the following criteria:
- Experience: Look for established companies with years in the industry, as they possess the knowledge and expertise in tool design and manufacturing.
- Quality Standards: Ensure the supplier follows strict quality control measures and certifications to guarantee the reliability of their molds.
- Customization Options: Choose a supplier that offers tailor-made solutions to fit your specific manufacturing needs.
- Technical Support: A supplier that provides robust technical support can be invaluable in optimizing the injection molding process.
Future Trends in Injection Molding
The injection molding industry is continuously evolving, driven by advancements in technology and increasing demand for sustainable practices. Some potential trends to watch include:
1. Industry 4.0 Integration
The adoption of smart manufacturing practices, including IoT and AI, is set to enhance the efficiency and precision of the injection molding process.
2. Sustainable Materials
With a growing emphasis on environmental responsibility, there is an increasing shift towards the use of biodegradable and recycled materials in injection molding.
3. Advanced Automation
Automation technologies are improving productivity and reducing labor costs, allowing for faster and more streamlined operations.
4. Additive Manufacturing Synergy
The integration of additive manufacturing (3D printing) with traditional molding processes is paving the way for innovative product designs and faster prototyping.
Conclusion
In conclusion, injection molding tools are indispensable in modern manufacturing. Their efficiency, precision, and versatility make them applicable across various industries, including automotive, electronics, and healthcare. As you explore the potential of injection molding, consider the benefits it brings to your production processes and the critical role played by high-quality mold design and fabrication.
For more information on injection molding and custom tooling solutions, visit deepmould.net and discover how we can assist you in maximizing your manufacturing capabilities through superior injection molding tools.