High Pressure Die Casting Manufacturers: Unlocking Efficiency and Quality in Metal Fabrication
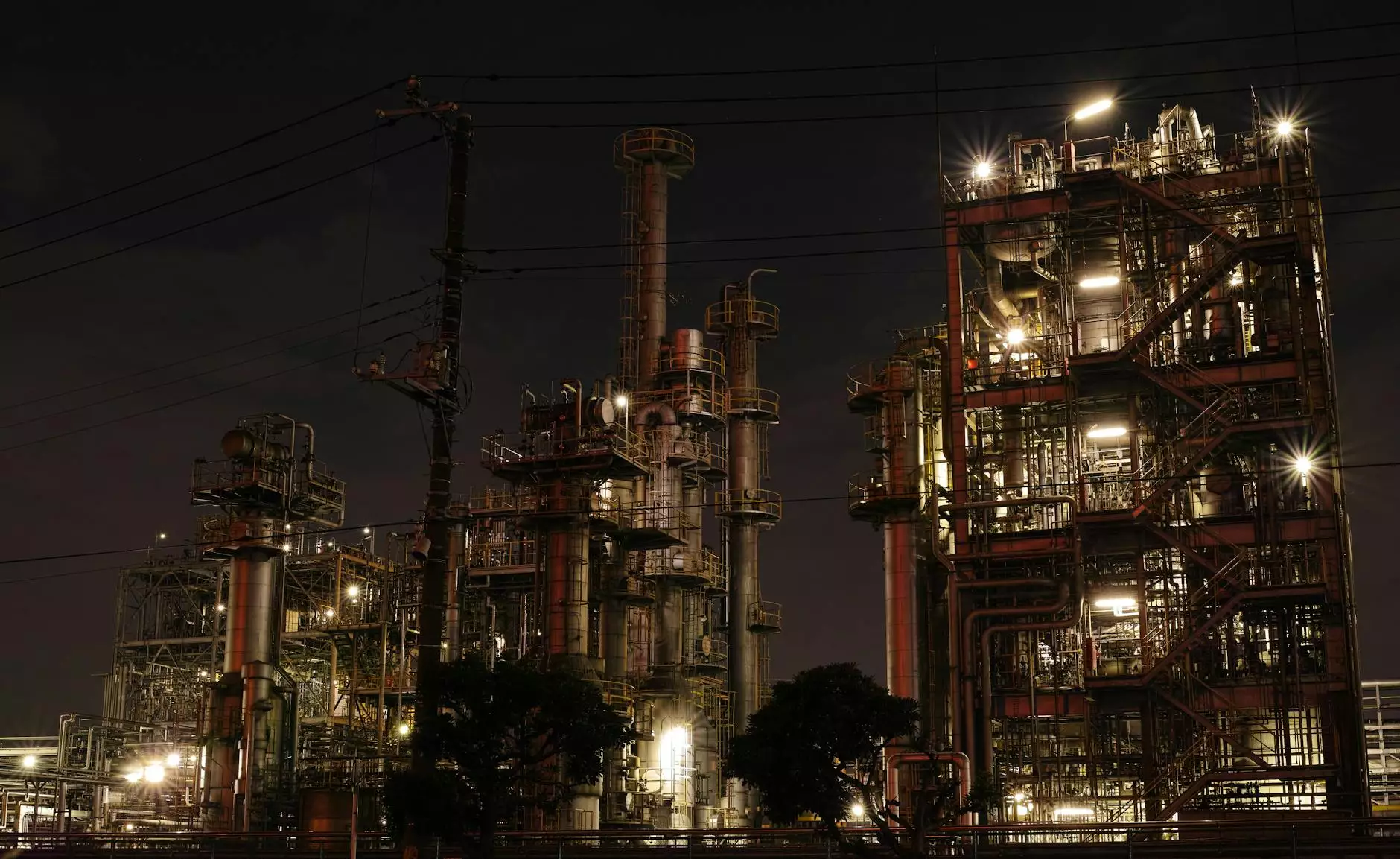
The manufacturing landscape has transformed significantly over the past few decades, particularly in the domain of metal fabrication. One of the most revolutionary advancements has been in the field of high pressure die casting. This technique, favored by many manufacturers for its precision and efficiency, has been championed by skilled high pressure die casting manufacturers around the world, setting the stage for transformative industrial growth.
Understanding High Pressure Die Casting
High pressure die casting is a manufacturing process that involves forcing molten metal into a mold cavity under high pressure. This practice is essential for creating complex shapes with excellent dimensional accuracy and smooth surface finishes, making it ideal for a range of applications. This method utilizes a variety of metals, most commonly aluminum, zinc, and magnesium alloys, which are known for their superior properties and durability.
Advantages of High Pressure Die Casting
The advantages offered by high pressure die casting manufacturers are numerous, contributing significantly to its popularity in the industry:
- Precision and Accuracy: The process allows for intricate designs with tight tolerances, making it suitable for high-precision components.
- Reduced Waste: The efficiency of the die casting process leads to minimized material waste compared to traditional methods.
- Cost-Effectiveness: High volume production can lead to lower per-unit costs, making it a financially viable option for mass production.
- Enhanced Surface Finish: Parts produced have a much smoother finish, often requiring little to no additional machining.
- Rapid Production Rates: High pressure die casting facilitates faster production rates, crucial for meeting market demands promptly.
The Role of High Pressure Die Casting Manufacturers
High pressure die casting manufacturers play a vital role in the industrial sector. They are responsible for not just executing the die casting process, but also ensuring that every component meets stringent quality standards.
Expertise in Material Selection
One of the critical aspects where these manufacturers excel is in material selection. The choice of metal can significantly influence the properties of the final product. High pressure die casting manufacturers possess extensive knowledge regarding which alloys are suitable for specific applications. Their expertise helps clients achieve desired outcomes, whether it be lightweight components for the automotive industry or durable parts for aerospace applications.
Quality Assurance Practices
Quality assurance is paramount in the metal fabrication industry. High pressure die casting manufacturers implement rigorous quality control processes throughout the production cycle. This may include:
- Material Testing: Ensuring the raw materials meet specified standards before entering the production line.
- Process Monitoring: Continuously monitoring the die casting process to maintain consistency and integrity.
- Final Inspection: Conducting thorough inspections of finished products to guarantee they meet the required specifications.
Applications of High Pressure Die Casting
High pressure die casting finds applications across various industries, highlighting its versatility:
Automotive Industry
The automotive sector is one of the largest users of die-cast components. Manufacturers create parts such as:
- Engine blocks and cylinder heads
- Transmission cases
- Structural components
Aerospace and Defense
In aerospace, weight efficiency and strength are critical. Die casting manufacturers provide:
- Critical components that must withstand harsh conditions
- Parts used in avionics systems
- Various casings and housings for sensitive instruments
Consumer Electronics
High pressure die casting is also widely used in the production of components for consumer electronics, providing:
- Lightweight housings
- Heat sinks for improved thermal management
- Frame structures that support electronic devices
Innovations in High Pressure Die Casting
The industry has seen significant innovations that have enhanced the capabilities of high pressure die casting manufacturers. Such advancements include:
Automation and Robotics
Automation plays a crucial role in modern die casting facilities, streamlining production processes and improving efficiency. Robots are increasingly used for:
- Loading molten metal into molds
- Removing finished parts from molds
- Quality checks and surface finishing tasks
3D Printing and Prototyping
Another innovative approach is the integration of 3D printing technologies in the development of casting molds. This allows manufacturers to:
- Rapidly prototype new designs
- Test complex geometries that would be difficult to achieve with conventional tooling
- Reduce lead times and costs associated with mold production